ಅನಿಲಾಕ್ಸ್ ರೋಲರ್ಗಳ ಬಳಕೆಯಲ್ಲಿ ಅನಿಲಾಕ್ಸ್ ರೋಲರ್ ಕೋಶಗಳ ಅಡಚಣೆಯು ವಾಸ್ತವವಾಗಿ ಅತ್ಯಂತ ಅನಿವಾರ್ಯ ವಿಷಯವಾಗಿದೆ,ಇದರ ಅಭಿವ್ಯಕ್ತಿಗಳನ್ನು ಎರಡು ಪ್ರಕರಣಗಳಾಗಿ ವಿಂಗಡಿಸಲಾಗಿದೆ: ಅನಿಲಾಕ್ಸ್ ರೋಲರ್ನ ಮೇಲ್ಮೈ ಅಡಚಣೆ (ಚಿತ್ರ.1) ಮತ್ತು ಅನಿಲಾಕ್ಸ್ ರೋಲರ್ ಕೋಶಗಳ ಅಡಚಣೆ (ಚಿತ್ರ. 2).
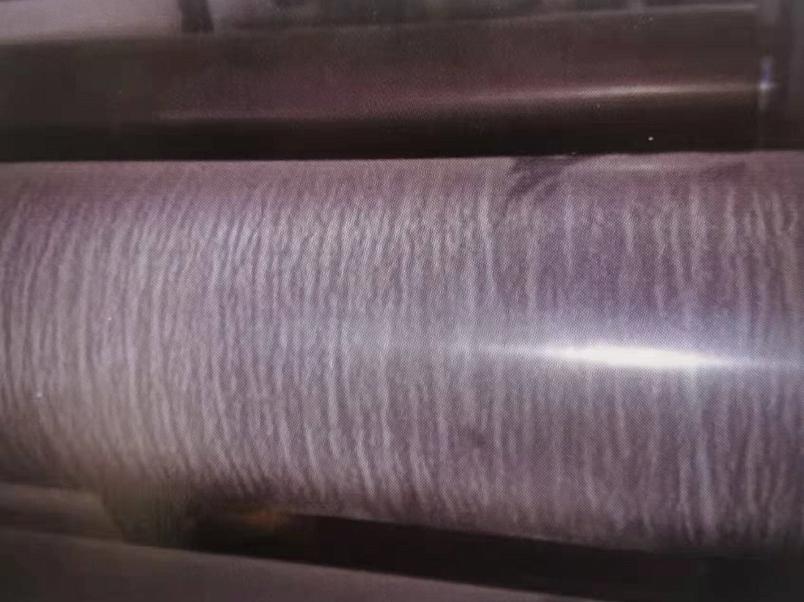
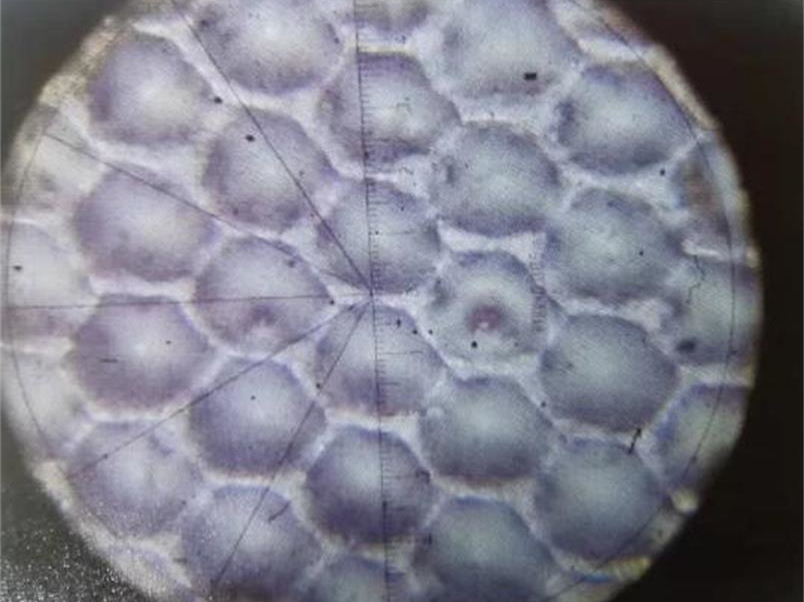
ಚಿತ್ರ .1
ಚಿತ್ರ .2
ವಿಶಿಷ್ಟವಾದ ಫ್ಲೆಕ್ಸೊ ಇಂಕ್ ವ್ಯವಸ್ಥೆಯು ಇಂಕ್ ಚೇಂಬರ್ (ಮುಚ್ಚಿದ ಇಂಕ್ ಫೀಡ್ ಸಿಸ್ಟಮ್), ಅನಿಲಾಕ್ಸ್ ರೋಲರ್, ಪ್ಲೇಟ್ ಸಿಲಿಂಡರ್ ಮತ್ತು ತಲಾಧಾರವನ್ನು ಒಳಗೊಂಡಿರುತ್ತದೆ. ಉತ್ತಮ ಗುಣಮಟ್ಟದ ಮುದ್ರಣಗಳನ್ನು ಪಡೆಯಲು ಇಂಕ್ ಚೇಂಬರ್, ಅನಿಲಾಕ್ಸ್ ರೋಲರ್ ಕೋಶಗಳು, ಪ್ರಿಂಟಿಂಗ್ ಪ್ಲೇಟ್ ಚುಕ್ಕೆಗಳ ಮೇಲ್ಮೈ ಮತ್ತು ತಲಾಧಾರದ ಮೇಲ್ಮೈ ನಡುವೆ ಸ್ಥಿರವಾದ ಶಾಯಿ ವರ್ಗಾವಣೆ ಪ್ರಕ್ರಿಯೆಯನ್ನು ಸ್ಥಾಪಿಸುವುದು ಅವಶ್ಯಕ. ಈ ಶಾಯಿ ವರ್ಗಾವಣೆ ಮಾರ್ಗದಲ್ಲಿ, ಅನಿಲಾಕ್ಸ್ ರೋಲ್ನಿಂದ ಪ್ಲೇಟ್ ಮೇಲ್ಮೈಗೆ ಶಾಯಿ ವರ್ಗಾವಣೆ ದರವು ಸರಿಸುಮಾರು 40% ಆಗಿದೆ, ಪ್ಲೇಟ್ನಿಂದ ತಲಾಧಾರಕ್ಕೆ ಶಾಯಿ ವರ್ಗಾವಣೆಯು ಸರಿಸುಮಾರು 50% ಆಗಿದೆ, ಅಂತಹ ಶಾಯಿ ಮಾರ್ಗ ವರ್ಗಾವಣೆಯು ಸರಳ ಭೌತಿಕ ವರ್ಗಾವಣೆಯಲ್ಲ, ಆದರೆ ಶಾಯಿ ವರ್ಗಾವಣೆ, ಶಾಯಿ ಒಣಗಿಸುವಿಕೆ ಮತ್ತು ಶಾಯಿ ಮರು ಕರಗಿಸುವಿಕೆಯನ್ನು ಒಳಗೊಂಡಂತೆ ಸಂಕೀರ್ಣ ಪ್ರಕ್ರಿಯೆಯಾಗಿದೆ ಎಂದು ಕಾಣಬಹುದು; ಫ್ಲೆಕ್ಸೊ ಮುದ್ರಣ ಯಂತ್ರದ ಮುದ್ರಣ ವೇಗವು ವೇಗವಾಗಿ ಮತ್ತು ವೇಗವಾಗಿ ಬರುತ್ತಿದ್ದಂತೆ, ಈ ಸಂಕೀರ್ಣ ಪ್ರಕ್ರಿಯೆಯು ಹೆಚ್ಚು ಹೆಚ್ಚು ಜಟಿಲವಾಗುವುದಲ್ಲದೆ, ಶಾಯಿ ಮಾರ್ಗ ಪ್ರಸರಣದಲ್ಲಿನ ಏರಿಳಿತಗಳ ಆವರ್ತನವು ವೇಗವಾಗಿ ಮತ್ತು ವೇಗವಾಗಿ ಆಗುತ್ತದೆ; ರಂಧ್ರಗಳ ಭೌತಿಕ ಗುಣಲಕ್ಷಣಗಳಿಗೆ ಅವಶ್ಯಕತೆಗಳು ಸಹ ಹೆಚ್ಚುತ್ತಿವೆ.
ಪಾಲಿಯುರೆಥೇನ್, ಅಕ್ರಿಲಿಕ್ ರಾಳ, ಇತ್ಯಾದಿ ಶಾಯಿಗಳಲ್ಲಿ, ಶಾಯಿ ಪದರದ ಅಂಟಿಕೊಳ್ಳುವಿಕೆ, ಸವೆತ ನಿರೋಧಕತೆ, ನೀರಿನ ಪ್ರತಿರೋಧ ಮತ್ತು ರಾಸಾಯನಿಕ ಪ್ರತಿರೋಧವನ್ನು ಸುಧಾರಿಸಲು ಅಡ್ಡ-ಸಂಪರ್ಕಿಸುವ ಕಾರ್ಯವಿಧಾನವನ್ನು ಹೊಂದಿರುವ ಪಾಲಿಮರ್ಗಳನ್ನು ವ್ಯಾಪಕವಾಗಿ ಬಳಸಲಾಗುತ್ತದೆ. ಅನಿಲಾಕ್ಸ್ ರೋಲರ್ ಕೋಶಗಳಲ್ಲಿನ ಶಾಯಿ ವರ್ಗಾವಣೆ ದರವು ಕೇವಲ 40% ಆಗಿರುವುದರಿಂದ, ಅಂದರೆ, ಕೋಶಗಳಲ್ಲಿನ ಹೆಚ್ಚಿನ ಶಾಯಿಯು ಸಂಪೂರ್ಣ ಮುದ್ರಣ ಪ್ರಕ್ರಿಯೆಯಲ್ಲಿ ಕೋಶಗಳ ಕೆಳಭಾಗದಲ್ಲಿಯೇ ಇರುತ್ತದೆ. ಶಾಯಿಯ ಒಂದು ಭಾಗವನ್ನು ಬದಲಾಯಿಸಿದರೂ ಸಹ, ಕೋಶಗಳಲ್ಲಿ ಶಾಯಿಯನ್ನು ಪೂರ್ಣಗೊಳಿಸುವುದು ಸುಲಭ. ರಾಳ ಅಡ್ಡ-ಸಂಪರ್ಕವನ್ನು ತಲಾಧಾರದ ಮೇಲ್ಮೈಯಲ್ಲಿ ಮಾಡಲಾಗುತ್ತದೆ, ಇದು ಅನಿಲಾಕ್ಸ್ ರೋಲ್ನ ಕೋಶಗಳ ಅಡಚಣೆಗೆ ಕಾರಣವಾಗುತ್ತದೆ.
ಅನಿಲಾಕ್ಸ್ ರೋಲರ್ನ ಮೇಲ್ಮೈ ನಿರ್ಬಂಧಿಸಲ್ಪಟ್ಟಿದೆ ಎಂದು ಅರ್ಥಮಾಡಿಕೊಳ್ಳುವುದು ಸುಲಭ. ಸಾಮಾನ್ಯವಾಗಿ, ಅನಿಲಾಕ್ಸ್ ರೋಲರ್ ಅನ್ನು ಅನುಚಿತವಾಗಿ ಬಳಸಲಾಗುತ್ತದೆ, ಇದರಿಂದಾಗಿ ಶಾಯಿಯನ್ನು ಕ್ಯೂರ್ ಮಾಡಲಾಗುತ್ತದೆ ಮತ್ತು ಅನಿಲಾಕ್ಸ್ ರೋಲರ್ನ ಮೇಲ್ಮೈಯಲ್ಲಿ ಅಡ್ಡ-ಲಿಂಕ್ ಮಾಡಲಾಗುತ್ತದೆ, ಇದರ ಪರಿಣಾಮವಾಗಿ ಅಡಚಣೆ ಉಂಟಾಗುತ್ತದೆ.
ಅನಿಲಾಕ್ಸ್ ರೋಲ್ ತಯಾರಕರಿಗೆ, ಸೆರಾಮಿಕ್ ಲೇಪನ ತಂತ್ರಜ್ಞಾನದ ಸಂಶೋಧನೆ ಮತ್ತು ಅಭಿವೃದ್ಧಿ, ಲೇಸರ್ ಅಪ್ಲಿಕೇಶನ್ ತಂತ್ರಜ್ಞಾನದ ಸುಧಾರಣೆ ಮತ್ತು ಅನಿಲಾಕ್ಸ್ ರೋಲ್ಗಳನ್ನು ಕೆತ್ತಿದ ನಂತರ ಸೆರಾಮಿಕ್ ಮೇಲ್ಮೈ ಸಂಸ್ಕರಣಾ ತಂತ್ರಜ್ಞಾನದ ಸುಧಾರಣೆಯು ಅನಿಲಾಕ್ಸ್ ರೋಲ್ ಕೋಶಗಳ ಅಡಚಣೆಯನ್ನು ಕಡಿಮೆ ಮಾಡುತ್ತದೆ. ಪ್ರಸ್ತುತ, ಸಾಮಾನ್ಯವಾಗಿ ಬಳಸುವ ವಿಧಾನಗಳು ಜಾಲರಿಯ ಗೋಡೆಯ ಅಗಲವನ್ನು ಕಡಿಮೆ ಮಾಡುವುದು, ಜಾಲರಿಯ ಒಳಗಿನ ಗೋಡೆಯ ಮೃದುತ್ವವನ್ನು ಸುಧಾರಿಸುವುದು ಮತ್ತು ಸೆರಾಮಿಕ್ ಲೇಪನದ ಸಾಂದ್ರತೆಯನ್ನು ಸುಧಾರಿಸುವುದು. .
ಮುದ್ರಣ ಉದ್ಯಮಗಳಿಗೆ, ಶಾಯಿಯ ಒಣಗಿಸುವ ವೇಗ, ಕರಗುವಿಕೆ ಮತ್ತು ಸ್ಕ್ವೀಜಿ ಬಿಂದುವಿನಿಂದ ಮುದ್ರಣ ಬಿಂದುವಿಗೆ ಇರುವ ಅಂತರವನ್ನು ಸಹ ಅನಿಲಾಕ್ಸ್ ರೋಲರ್ ಕೋಶಗಳ ಅಡಚಣೆಯನ್ನು ಕಡಿಮೆ ಮಾಡಲು ಸರಿಹೊಂದಿಸಬಹುದು.
ತುಕ್ಕು ಹಿಡಿಯುವುದು
ಚಿತ್ರ 3 ರಲ್ಲಿ ತೋರಿಸಿರುವಂತೆ, ಅನಿಲಾಕ್ಸ್ ರೋಲರ್ನ ಮೇಲ್ಮೈಯಲ್ಲಿ ಬಿಂದುವಿನಂತಹ ಮುಂಚಾಚಿರುವಿಕೆಗಳ ವಿದ್ಯಮಾನವನ್ನು ತುಕ್ಕು ಸೂಚಿಸುತ್ತದೆ. ಶುಚಿಗೊಳಿಸುವ ಏಜೆಂಟ್ ಸೆರಾಮಿಕ್ ಅಂತರದ ಉದ್ದಕ್ಕೂ ಕೆಳಗಿನ ಪದರವನ್ನು ಒಳನುಸುಳಿ, ಕೆಳಗಿನ ಲೋಹದ ಬೇಸ್ ರೋಲರ್ ಅನ್ನು ತುಕ್ಕು ಹಿಡಿಯುವುದು ಮತ್ತು ಒಳಗಿನಿಂದ ಸೆರಾಮಿಕ್ ಪದರವನ್ನು ಒಡೆಯುವುದರಿಂದ ತುಕ್ಕು ಉಂಟಾಗುತ್ತದೆ, ಇದರಿಂದಾಗಿ ಅನಿಲಾಕ್ಸ್ ರೋಲರ್ಗೆ ಹಾನಿಯಾಗುತ್ತದೆ (ಚಿತ್ರ 4, ಚಿತ್ರ 5).
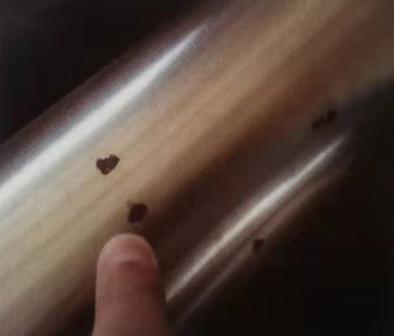
ಚಿತ್ರ 3
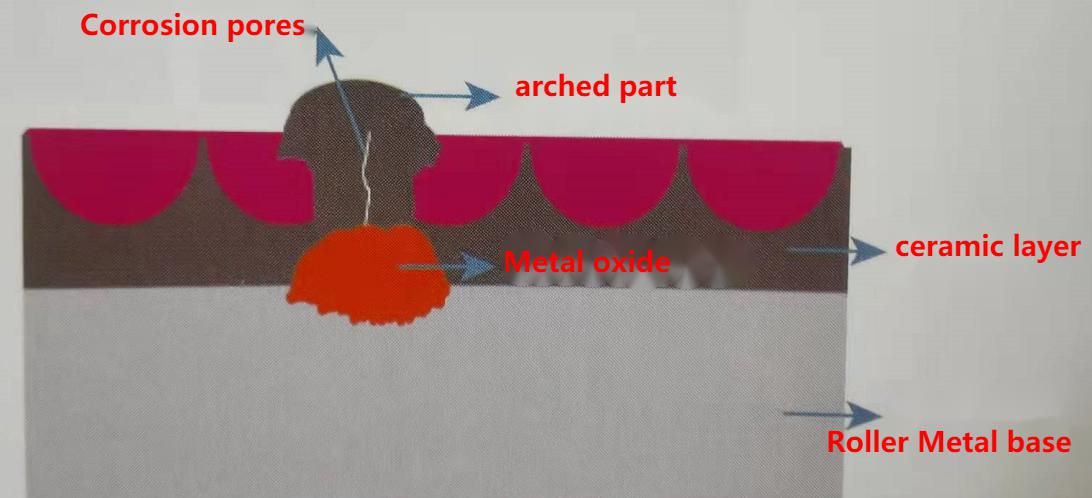
ಚಿತ್ರ 4
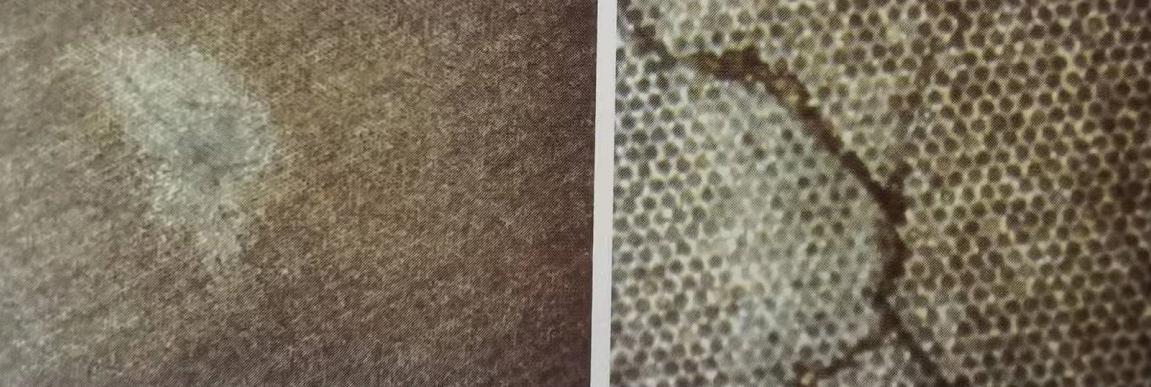
ಸೂಕ್ಷ್ಮದರ್ಶಕದ ಅಡಿಯಲ್ಲಿ ಚಿತ್ರ 5 ಸವೆತ
ತುಕ್ಕು ರಚನೆಗೆ ಕಾರಣಗಳು ಈ ಕೆಳಗಿನಂತಿವೆ:
① ಲೇಪನದ ರಂಧ್ರಗಳು ದೊಡ್ಡದಾಗಿರುತ್ತವೆ ಮತ್ತು ದ್ರವವು ರಂಧ್ರಗಳ ಮೂಲಕ ಬೇಸ್ ರೋಲರ್ ಅನ್ನು ತಲುಪಬಹುದು, ಇದು ಬೇಸ್ ರೋಲರ್ನ ತುಕ್ಕುಗೆ ಕಾರಣವಾಗುತ್ತದೆ.
② ಬಲವಾದ ಆಮ್ಲಗಳು ಮತ್ತು ಬಲವಾದ ಕ್ಷಾರಗಳಂತಹ ಶುಚಿಗೊಳಿಸುವ ಏಜೆಂಟ್ಗಳ ದೀರ್ಘಾವಧಿಯ ಬಳಕೆ, ಬಳಕೆಯ ನಂತರ ಸಕಾಲಿಕ ಸ್ನಾನ ಮತ್ತು ಗಾಳಿಯಲ್ಲಿ ಒಣಗಿಸದೆ.
③ ಶುಚಿಗೊಳಿಸುವ ವಿಧಾನವು ತಪ್ಪಾಗಿದೆ, ವಿಶೇಷವಾಗಿ ಉಪಕರಣಗಳನ್ನು ದೀರ್ಘಕಾಲದವರೆಗೆ ಸ್ವಚ್ಛಗೊಳಿಸುವಾಗ.
④ ಶೇಖರಣಾ ವಿಧಾನವು ತಪ್ಪಾಗಿದೆ, ಮತ್ತು ಇದನ್ನು ದೀರ್ಘಕಾಲದವರೆಗೆ ಆರ್ದ್ರ ವಾತಾವರಣದಲ್ಲಿ ಸಂಗ್ರಹಿಸಲಾಗುತ್ತದೆ.
⑤ ಶಾಯಿ ಅಥವಾ ಸೇರ್ಪಡೆಗಳ pH ಮೌಲ್ಯವು ತುಂಬಾ ಹೆಚ್ಚಾಗಿದೆ, ವಿಶೇಷವಾಗಿ ನೀರು ಆಧಾರಿತ ಶಾಯಿ.
⑥ ಅನುಸ್ಥಾಪನೆ ಮತ್ತು ಡಿಸ್ಅಸೆಂಬಲ್ ಪ್ರಕ್ರಿಯೆಯ ಸಮಯದಲ್ಲಿ ಅನಿಲಾಕ್ಸ್ ರೋಲರ್ ಪ್ರಭಾವಿತವಾಗುತ್ತದೆ, ಇದರ ಪರಿಣಾಮವಾಗಿ ಸೆರಾಮಿಕ್ ಪದರದ ಅಂತರವು ಬದಲಾಗುತ್ತದೆ.
ತುಕ್ಕು ಹಿಡಿಯುವಿಕೆ ಮತ್ತು ಅನಿಲಾಕ್ಸ್ ರೋಲ್ಗೆ ಅಂತಿಮವಾಗಿ ಹಾನಿಯಾಗುವ ನಡುವಿನ ದೀರ್ಘ ಸಮಯದಿಂದಾಗಿ ಆರಂಭಿಕ ಕಾರ್ಯಾಚರಣೆಯನ್ನು ಹೆಚ್ಚಾಗಿ ಕಡೆಗಣಿಸಲಾಗುತ್ತದೆ. ಆದ್ದರಿಂದ, ಸೆರಾಮಿಕ್ ಅನಿಲಾಕ್ಸ್ ರೋಲರ್ನ ಬ್ಯಾಗಿಂಗ್ ವಿದ್ಯಮಾನವನ್ನು ಕಂಡುಕೊಂಡ ನಂತರ, ಕಮಾನಿನ ಕಾರಣವನ್ನು ತನಿಖೆ ಮಾಡಲು ನೀವು ಸೆರಾಮಿಕ್ ಅನಿಲಾಕ್ಸ್ ರೋಲರ್ ಪೂರೈಕೆದಾರರನ್ನು ಸಮಯಕ್ಕೆ ಸರಿಯಾಗಿ ಸಂಪರ್ಕಿಸಬೇಕು.
ಸುತ್ತಳತೆಯ ಗೀರುಗಳು
ಅನಿಲಾಕ್ಸ್ ರೋಲ್ಗಳ ಗೀರುಗಳು ಅನಿಲಾಕ್ಸ್ ರೋಲ್ಗಳ ಬಾಳಿಕೆ ಮೇಲೆ ಪರಿಣಾಮ ಬೀರುವ ಸಾಮಾನ್ಯ ಸಮಸ್ಯೆಗಳಾಗಿವೆ.(ಚಿತ್ರ 6)ಏಕೆಂದರೆ ಅನಿಲಾಕ್ಸ್ ರೋಲರ್ ಮತ್ತು ಡಾಕ್ಟರ್ ಬ್ಲೇಡ್ ನಡುವಿನ ಕಣಗಳು ಒತ್ತಡದ ಕ್ರಿಯೆಯ ಅಡಿಯಲ್ಲಿ ಅನಿಲಾಕ್ಸ್ ರೋಲರ್ನ ಮೇಲ್ಮೈ ಸೆರಾಮಿಕ್ಗಳನ್ನು ಮುರಿದು, ಮುದ್ರಣ ಚಾಲನೆಯಲ್ಲಿರುವ ದಿಕ್ಕಿನಲ್ಲಿ ಎಲ್ಲಾ ಜಾಲರಿಯ ಗೋಡೆಗಳನ್ನು ತೆರೆದು ತೋಡು ರೂಪಿಸುತ್ತವೆ. ಮುದ್ರಣದ ಕಾರ್ಯಕ್ಷಮತೆಯು ಗಾಢವಾದ ರೇಖೆಗಳ ನೋಟವಾಗಿದೆ.
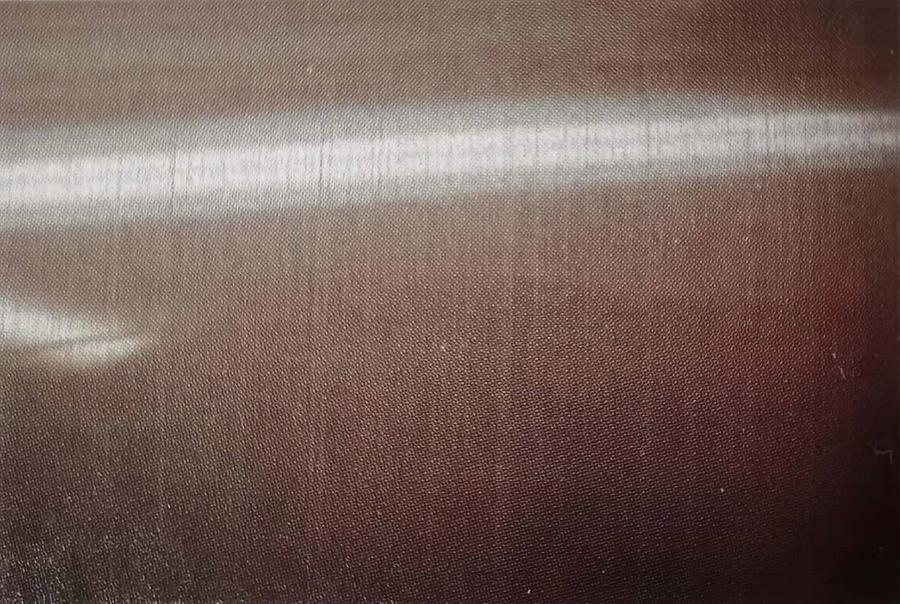
ಚಿತ್ರ 6 ಗೀರುಗಳಿರುವ ಅನಿಲಾಕ್ಸ್ ರೋಲ್
ಗೀರುಗಳ ಮೂಲ ಸಮಸ್ಯೆಯೆಂದರೆ ಡಾಕ್ಟರ್ ಬ್ಲೇಡ್ ಮತ್ತು ಅನಿಲಾಕ್ಸ್ ರೋಲರ್ ನಡುವಿನ ಒತ್ತಡದಲ್ಲಿನ ಬದಲಾವಣೆ, ಇದರಿಂದಾಗಿ ಮೂಲ ಮುಖಾಮುಖಿ ಒತ್ತಡವು ಸ್ಥಳೀಯ ಪಾಯಿಂಟ್-ಟು-ಫೇಸ್ ಒತ್ತಡವಾಗುತ್ತದೆ; ಮತ್ತು ಹೆಚ್ಚಿನ ಮುದ್ರಣ ವೇಗವು ಒತ್ತಡವನ್ನು ತೀವ್ರವಾಗಿ ಹೆಚ್ಚಿಸಲು ಕಾರಣವಾಗುತ್ತದೆ ಮತ್ತು ವಿನಾಶಕಾರಿ ಶಕ್ತಿ ಅದ್ಭುತವಾಗಿದೆ. (ಚಿತ್ರ 7)
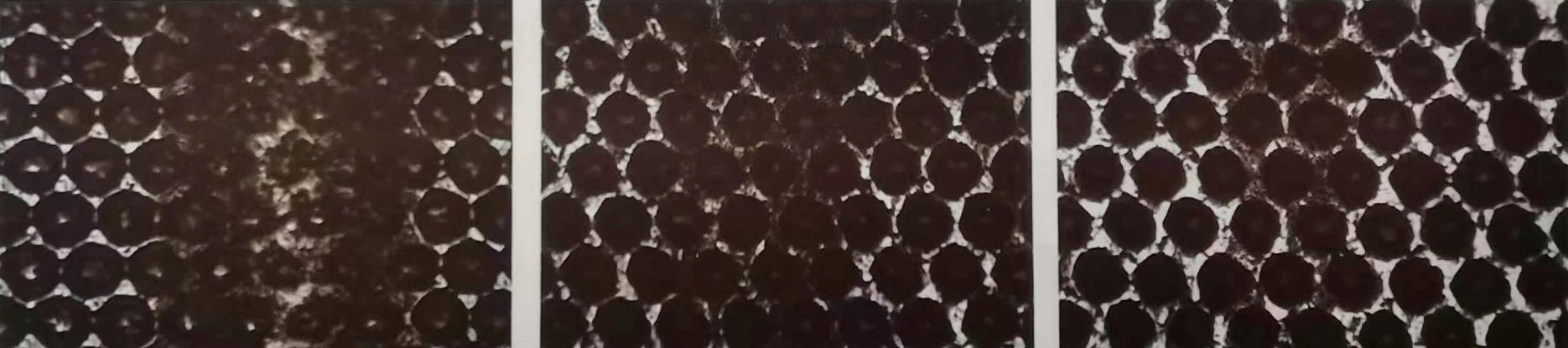
ಚಿತ್ರ 7 ತೀವ್ರ ಗೀರುಗಳು
ಸಾಮಾನ್ಯ ಗೀರುಗಳು
ಸಣ್ಣ ಗೀರುಗಳು
ಸಾಮಾನ್ಯವಾಗಿ, ಮುದ್ರಣದ ವೇಗವನ್ನು ಅವಲಂಬಿಸಿ, ಮುದ್ರಣದ ಮೇಲೆ ಪರಿಣಾಮ ಬೀರುವ ಗೀರುಗಳು 3 ರಿಂದ 10 ನಿಮಿಷಗಳಲ್ಲಿ ರೂಪುಗೊಳ್ಳುತ್ತವೆ. ಈ ಒತ್ತಡವನ್ನು ಬದಲಾಯಿಸುವ ಹಲವು ಅಂಶಗಳಿವೆ, ಮುಖ್ಯವಾಗಿ ಹಲವಾರು ಅಂಶಗಳಿಂದ: ಅನಿಲಾಕ್ಸ್ ರೋಲರ್ ಸ್ವತಃ, ಡಾಕ್ಟರ್ ಬ್ಲೇಡ್ ವ್ಯವಸ್ಥೆಯ ಶುಚಿಗೊಳಿಸುವಿಕೆ ಮತ್ತು ನಿರ್ವಹಣೆ, ಡಾಕ್ಟರ್ ಬ್ಲೇಡ್ನ ಗುಣಮಟ್ಟ ಮತ್ತು ಸ್ಥಾಪನೆ ಮತ್ತು ಬಳಕೆ ಮತ್ತು ಉಪಕರಣಗಳ ವಿನ್ಯಾಸ ದೋಷಗಳು.
1. ಅನಿಲಾಕ್ಸ್ ರೋಲರ್ ಸ್ವತಃ
(1) ಕೆತ್ತನೆಯ ನಂತರ ಸೆರಾಮಿಕ್ ಅನಿಲಾಕ್ಸ್ ರೋಲರ್ನ ಮೇಲ್ಮೈ ಚಿಕಿತ್ಸೆ ಸಾಕಾಗುವುದಿಲ್ಲ, ಮತ್ತು ಮೇಲ್ಮೈ ಒರಟಾಗಿರುತ್ತದೆ ಮತ್ತು ಸ್ಕ್ರಾಪರ್ ಮತ್ತು ಸ್ಕ್ರಾಪರ್ನ ಬ್ಲೇಡ್ ಅನ್ನು ಸ್ಕ್ರಾಚ್ ಮಾಡಲು ಸುಲಭವಾಗಿದೆ.
ಅನಿಲಾಕ್ಸ್ ರೋಲರ್ನೊಂದಿಗಿನ ಸಂಪರ್ಕ ಮೇಲ್ಮೈ ಬದಲಾಗಿದೆ, ಒತ್ತಡವನ್ನು ಹೆಚ್ಚಿಸುತ್ತದೆ, ಒತ್ತಡವನ್ನು ಗುಣಿಸುತ್ತದೆ ಮತ್ತು ಹೆಚ್ಚಿನ ವೇಗದ ಕಾರ್ಯಾಚರಣೆಯ ಸ್ಥಿತಿಯಲ್ಲಿ ಜಾಲರಿಯನ್ನು ಮುರಿಯುತ್ತದೆ.
ಉಬ್ಬು ರೋಲರ್ನ ಮೇಲ್ಮೈ ಗೀರುಗಳನ್ನು ರೂಪಿಸುತ್ತದೆ.
(2) ಹೊಳಪು ನೀಡುವ ಮತ್ತು ಸೂಕ್ಷ್ಮವಾಗಿ ರುಬ್ಬುವ ಪ್ರಕ್ರಿಯೆಯ ಸಮಯದಲ್ಲಿ ಆಳವಾದ ಹೊಳಪು ನೀಡುವ ರೇಖೆಯು ರೂಪುಗೊಳ್ಳುತ್ತದೆ. ಅನಿಲಾಕ್ಸ್ ರೋಲ್ ಅನ್ನು ತಲುಪಿಸಿದಾಗ ಈ ಪರಿಸ್ಥಿತಿ ಸಾಮಾನ್ಯವಾಗಿ ಇರುತ್ತದೆ ಮತ್ತು ಲಘುವಾಗಿ ಹೊಳಪು ಮಾಡಿದ ರೇಖೆಯು ಮುದ್ರಣದ ಮೇಲೆ ಪರಿಣಾಮ ಬೀರುವುದಿಲ್ಲ. ಈ ಸಂದರ್ಭದಲ್ಲಿ, ಮುದ್ರಣ ಪರಿಶೀಲನೆಯನ್ನು ಯಂತ್ರದಲ್ಲಿ ನಡೆಸಬೇಕಾಗುತ್ತದೆ.
2. ಡಾಕ್ಟರ್ ಬ್ಲೇಡ್ ವ್ಯವಸ್ಥೆಯ ಶುಚಿಗೊಳಿಸುವಿಕೆ ಮತ್ತು ನಿರ್ವಹಣೆ
(1) ಚೇಂಬರ್ ಡಾಕ್ಟರ್ ಬ್ಲೇಡ್ನ ಮಟ್ಟವನ್ನು ಸರಿಪಡಿಸಲಾಗಿದ್ದರೂ, ಕಳಪೆ ಮಟ್ಟದ ಚೇಂಬರ್ ಡಾಕ್ಟರ್ ಬ್ಲೇಡ್ ಅಸಮ ಒತ್ತಡವನ್ನು ಉಂಟುಮಾಡುತ್ತದೆ. (ಚಿತ್ರ 8)
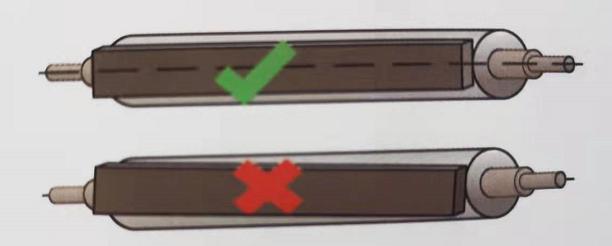
ಚಿತ್ರ 8
(2) ಡಾಕ್ಟರ್ ಬ್ಲೇಡ್ ಚೇಂಬರ್ ಅನ್ನು ಲಂಬವಾಗಿ ಇರಿಸಿದರೂ, ಲಂಬವಲ್ಲದ ಇಂಕ್ ಚೇಂಬರ್ ಬ್ಲೇಡ್ನ ಸಂಪರ್ಕ ಮೇಲ್ಮೈಯನ್ನು ಹೆಚ್ಚಿಸುತ್ತದೆ. ಗಂಭೀರವಾಗಿ, ಇದು ಅನಿಲಾಕ್ಸ್ ರೋಲರ್ಗೆ ನೇರವಾಗಿ ಹಾನಿಯನ್ನುಂಟುಮಾಡುತ್ತದೆ. ಚಿತ್ರ 9
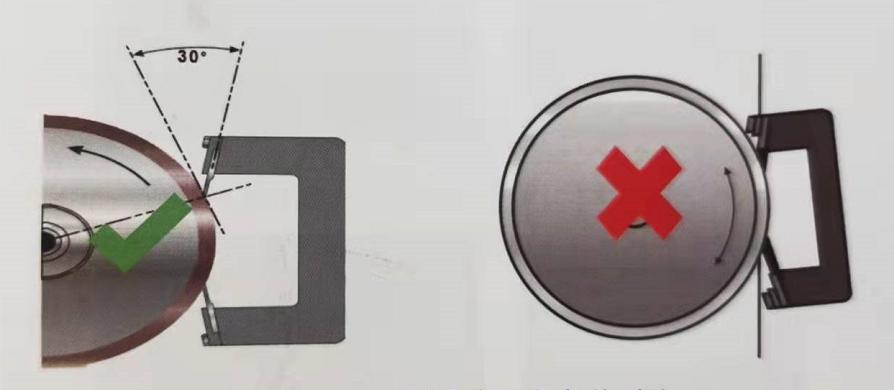
ಚಿತ್ರ 9
(3) ಚೇಂಬರ್ ಡಾಕ್ಟರ್ ಬ್ಲೇಡ್ ವ್ಯವಸ್ಥೆಯನ್ನು ಸ್ವಚ್ಛಗೊಳಿಸುವುದು ಬಹಳ ಮುಖ್ಯ, ಡಾಕ್ಟರ್ ಬ್ಲೇಡ್ ಮತ್ತು ಅನಿಲಾಕ್ಸ್ ರೋಲರ್ ನಡುವೆ ಸಿಲುಕಿಕೊಳ್ಳುವ ಕಲ್ಮಶಗಳು ಶಾಯಿ ವ್ಯವಸ್ಥೆಯನ್ನು ಪ್ರವೇಶಿಸುವುದನ್ನು ತಡೆಯಿರಿ. ಇದು ಒತ್ತಡದಲ್ಲಿ ಬದಲಾವಣೆಗಳಿಗೆ ಕಾರಣವಾಗುತ್ತದೆ. ಒಣ ಶಾಯಿ ಕೂಡ ತುಂಬಾ ಅಪಾಯಕಾರಿ.
3. ಡಾಕ್ಟರ್ ಬ್ಲೇಡ್ನ ಸ್ಥಾಪನೆ ಮತ್ತು ಬಳಕೆ
(1) ಬ್ಲೇಡ್ಗೆ ಹಾನಿಯಾಗದಂತೆ, ಬ್ಲೇಡ್ ಅಲೆಗಳಿಲ್ಲದೆ ನೇರವಾಗಿರುವಂತೆ ಮತ್ತು ಬ್ಲೇಡ್ ಹೋಲ್ಡರ್ನೊಂದಿಗೆ ಸಂಪೂರ್ಣವಾಗಿ ಸಂಯೋಜಿಸಲ್ಪಟ್ಟಿರುವಂತೆ ಚೇಂಬರ್ ಡಾಕ್ಟರ್ ಬ್ಲೇಡ್ ಅನ್ನು ಸರಿಯಾಗಿ ಸ್ಥಾಪಿಸಿ, ಉದಾಹರಣೆಗೆ
ಚಿತ್ರ 10 ರಲ್ಲಿ ತೋರಿಸಿರುವಂತೆ, ಅನಿಲಾಕ್ಸ್ ರೋಲರ್ನ ಮೇಲ್ಮೈಯಲ್ಲಿಯೂ ಒತ್ತಡ ಇರುವಂತೆ ನೋಡಿಕೊಳ್ಳಿ.
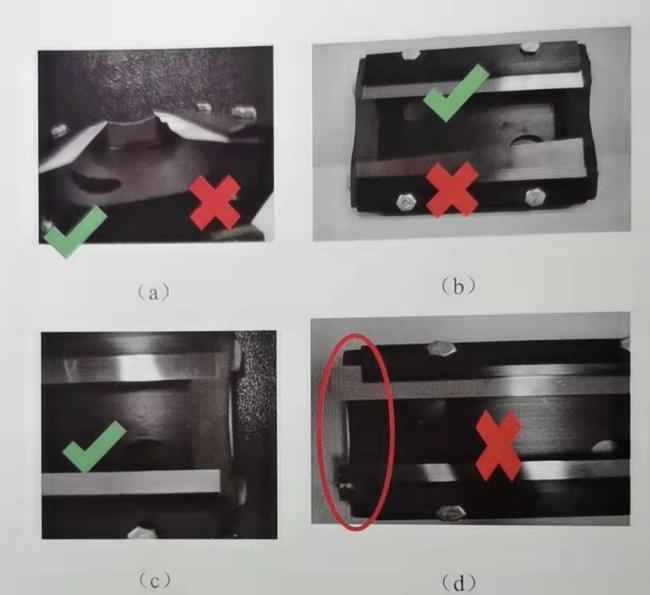
ಚಿತ್ರ 10
(2) ಉತ್ತಮ ಗುಣಮಟ್ಟದ ಸ್ಕ್ರಾಪರ್ಗಳನ್ನು ಬಳಸಿ. ಚಿತ್ರ 11 (ಎ) ನಲ್ಲಿ ತೋರಿಸಿರುವಂತೆ ಉತ್ತಮ ಗುಣಮಟ್ಟದ ಸ್ಕ್ರಾಪರ್ ಉಕ್ಕು ಬಿಗಿಯಾದ ಆಣ್ವಿಕ ರಚನೆಯನ್ನು ಹೊಂದಿದೆ, ಸವೆದ ನಂತರ ಕಣಗಳು ಚಿಕ್ಕದಾಗಿರುತ್ತವೆ ಮತ್ತು ಏಕರೂಪವಾಗಿರುತ್ತವೆ; ಕಡಿಮೆ ಗುಣಮಟ್ಟದ ಸ್ಕ್ರಾಪರ್ ಉಕ್ಕಿನ ಆಣ್ವಿಕ ರಚನೆಯು ಸಾಕಷ್ಟು ಬಿಗಿಯಾಗಿರುವುದಿಲ್ಲ ಮತ್ತು ಸವೆದ ನಂತರ ಕಣಗಳು ದೊಡ್ಡದಾಗಿರುತ್ತವೆ, ಚಿತ್ರ 11 (ಬಿ) ನಲ್ಲಿ ತೋರಿಸಿರುವಂತೆ.
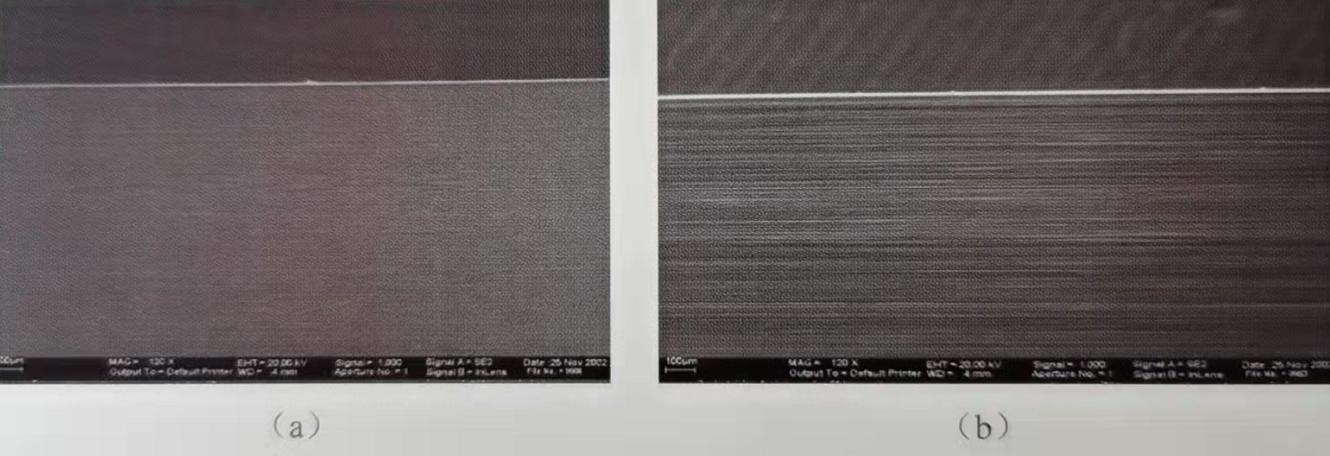
ಚಿತ್ರ 11
(3) ಬ್ಲೇಡ್ ಚಾಕುವನ್ನು ಸಮಯಕ್ಕೆ ಬದಲಾಯಿಸಿ. ಬದಲಾಯಿಸುವಾಗ, ಚಾಕುವಿನ ಅಂಚನ್ನು ಬಡಿದುಕೊಳ್ಳದಂತೆ ರಕ್ಷಿಸಲು ಗಮನ ಕೊಡಿ. ಅನಿಲಾಕ್ಸ್ ರೋಲರ್ನ ವಿಭಿನ್ನ ಸಾಲಿನ ಸಂಖ್ಯೆಯನ್ನು ಬದಲಾಯಿಸುವಾಗ, ನೀವು ಬ್ಲೇಡ್ ಚಾಕುವನ್ನು ಬದಲಾಯಿಸಬೇಕು. ವಿಭಿನ್ನ ಸಾಲಿನ ಸಂಖ್ಯೆಗಳೊಂದಿಗೆ ಅನಿಲಾಕ್ಸ್ ರೋಲರ್ನ ಉಡುಗೆ ಮಟ್ಟವು ಅಸಮಂಜಸವಾಗಿದೆ, ಚಿತ್ರ 12 ರಲ್ಲಿ ತೋರಿಸಿರುವಂತೆ, ಎಡ ಚಿತ್ರವು ಕಡಿಮೆ ರೇಖೆಯ ಸಂಖ್ಯೆಯ ಪರದೆಯಾಗಿದೆ ಬ್ಲೇಡ್ ಚಾಕುವಿನ ಮೇಲೆ ಬ್ಲೇಡ್ ಚಾಕುವನ್ನು ರುಬ್ಬುವುದು ಹಾನಿಗೊಳಗಾದ ಅಂತ್ಯದ ಸ್ಥಿತಿ, ಬಲಭಾಗದಲ್ಲಿರುವ ಚಿತ್ರವು ಬ್ಲೇಡ್ ಚಾಕುವಿಗೆ ಹೈ ಲೈನ್ ಎಣಿಕೆ ಅನಿಲಾಕ್ಸ್ ರೋಲರ್ನ ಧರಿಸಿರುವ ಅಂತ್ಯದ ಸ್ಥಿತಿಯನ್ನು ತೋರಿಸುತ್ತದೆ. ಡಾಕ್ಟರ್ ಬ್ಲೇಡ್ ಮತ್ತು ಅನಿಲಾಕ್ಸ್ ರೋಲರ್ ನಡುವಿನ ಸಂಪರ್ಕ ಮೇಲ್ಮೈ ಹೊಂದಿಕೆಯಾಗದ ಉಡುಗೆ ಮಟ್ಟಗಳೊಂದಿಗೆ ಬದಲಾಗುತ್ತದೆ, ಇದು ಒತ್ತಡದ ಬದಲಾವಣೆಗಳು ಮತ್ತು ಗೀರುಗಳನ್ನು ಉಂಟುಮಾಡುತ್ತದೆ.
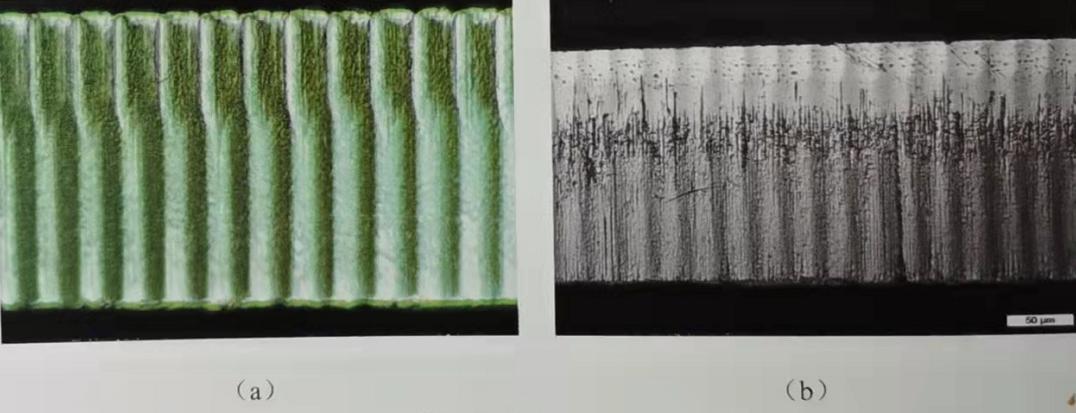
ಚಿತ್ರ 12
(4) ಸ್ಕ್ವೀಜಿಯ ಒತ್ತಡವು ಹಗುರವಾಗಿರಬೇಕು ಮತ್ತು ಸ್ಕ್ವೀಜಿಯ ಅತಿಯಾದ ಒತ್ತಡವು ಸ್ಕ್ವೀಜಿ ಮತ್ತು ಅನಿಲಾಕ್ಸ್ ರೋಲರ್ನ ಸಂಪರ್ಕ ಪ್ರದೇಶ ಮತ್ತು ಕೋನವನ್ನು ಬದಲಾಯಿಸುತ್ತದೆ, ಚಿತ್ರ 13 ರಲ್ಲಿ ತೋರಿಸಿರುವಂತೆ. ಕಲ್ಮಶಗಳನ್ನು ಒಳಸೇರಿಸುವುದು ಸುಲಭ, ಮತ್ತು ಪ್ರವೇಶಿಸಿದ ಕಲ್ಮಶಗಳು ಒತ್ತಡವನ್ನು ಬದಲಾಯಿಸಿದ ನಂತರ ಗೀರುಗಳನ್ನು ಉಂಟುಮಾಡುತ್ತವೆ. ಅಸಮಂಜಸ ಒತ್ತಡವನ್ನು ಬಳಸಿದಾಗ, ಬದಲಿ ಸ್ಕ್ರಾಪರ್ನ ಅಡ್ಡ ವಿಭಾಗದಲ್ಲಿ ಧರಿಸಿರುವ ಲೋಹದ ಬಾಲಗಳು ಚಿತ್ರ 14 ಇರುತ್ತವೆ. ಅದು ಬಿದ್ದ ನಂತರ, ಅದು ಸ್ಕ್ರಾಪರ್ ಮತ್ತು ಅನಿಲಾಕ್ಸ್ ರೋಲರ್ ನಡುವೆ ಸಿಕ್ಕಿಹಾಕಿಕೊಳ್ಳುತ್ತದೆ, ಇದು ಅನಿಲಾಕ್ಸ್ ರೋಲರ್ನಲ್ಲಿ ಗೀರುಗಳನ್ನು ಉಂಟುಮಾಡಬಹುದು.
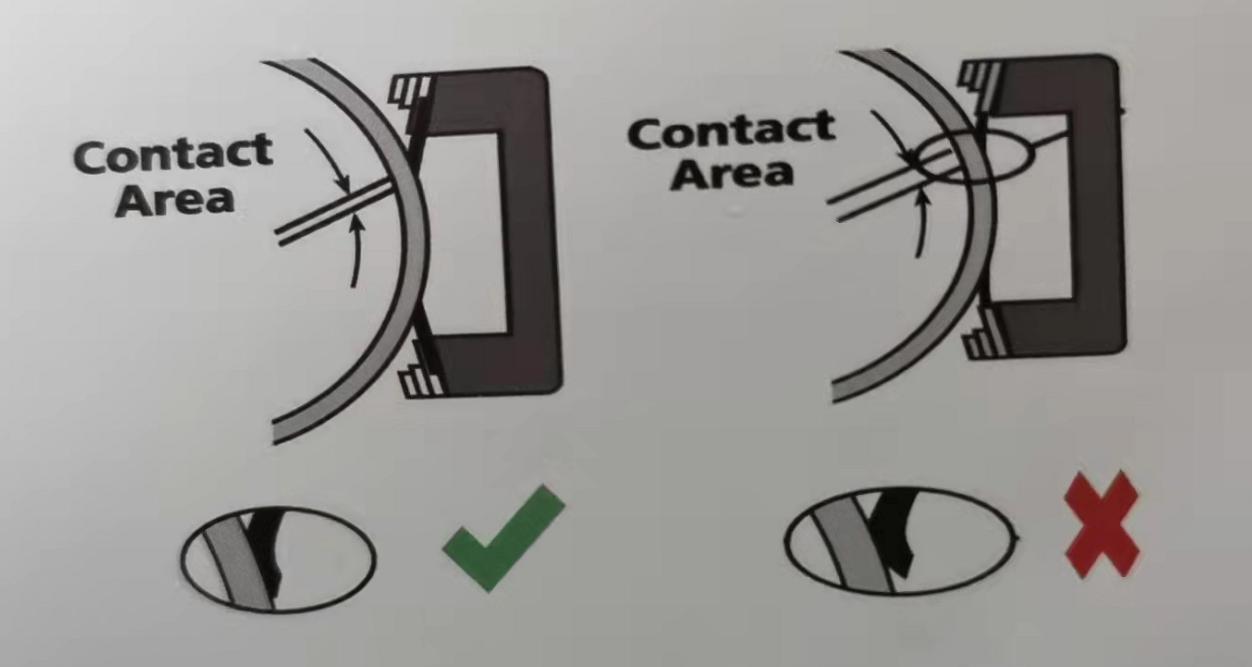
ಚಿತ್ರ 13
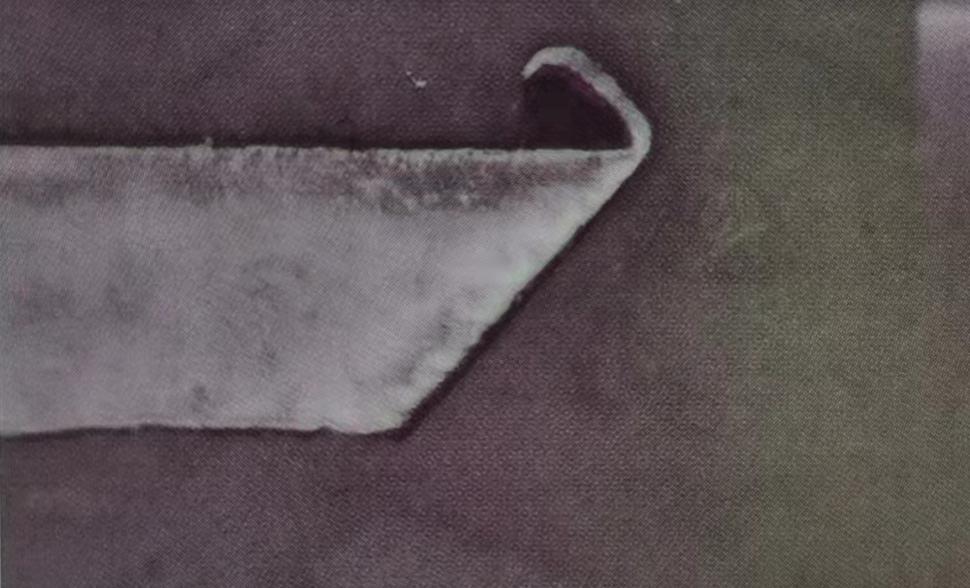
ಚಿತ್ರ 14
4. ಉಪಕರಣಗಳ ವಿನ್ಯಾಸ ದೋಷಗಳು
ವಿನ್ಯಾಸದ ದೋಷಗಳು ಸುಲಭವಾಗಿ ಗೀರುಗಳಿಗೆ ಕಾರಣವಾಗಬಹುದು, ಉದಾಹರಣೆಗೆ ಇಂಕ್ ಬ್ಲಾಕ್ನ ವಿನ್ಯಾಸ ಮತ್ತು ಅನಿಲಾಕ್ಸ್ ರೋಲ್ನ ವ್ಯಾಸದ ನಡುವಿನ ಹೊಂದಾಣಿಕೆಯಿಲ್ಲದಿರುವುದು. ಸ್ಕ್ವೀಜಿ ಕೋನದ ಅಸಮಂಜಸ ವಿನ್ಯಾಸ, ಅನಿಲಾಕ್ಸ್ ರೋಲರ್ನ ವ್ಯಾಸ ಮತ್ತು ಉದ್ದದ ನಡುವಿನ ಅಸಂಗತತೆ ಇತ್ಯಾದಿಗಳು ಅನಿಶ್ಚಿತ ಅಂಶಗಳನ್ನು ತರುತ್ತವೆ. ಅನಿಲಾಕ್ಸ್ ರೋಲ್ನ ಸುತ್ತಳತೆಯ ದಿಕ್ಕಿನಲ್ಲಿ ಗೀರುಗಳ ಸಮಸ್ಯೆ ತುಂಬಾ ಜಟಿಲವಾಗಿದೆ ಎಂದು ಕಾಣಬಹುದು. ಒತ್ತಡದಲ್ಲಿನ ಬದಲಾವಣೆಗಳು, ಸಮಯಕ್ಕೆ ಸರಿಯಾಗಿ ಸ್ವಚ್ಛಗೊಳಿಸುವಿಕೆ ಮತ್ತು ನಿರ್ವಹಣೆ, ಸರಿಯಾದ ಸ್ಕ್ರಾಪರ್ ಅನ್ನು ಆಯ್ಕೆ ಮಾಡುವುದು ಮತ್ತು ಉತ್ತಮ ಮತ್ತು ಕ್ರಮಬದ್ಧವಾದ ಕಾರ್ಯಾಚರಣೆಯ ಅಭ್ಯಾಸಗಳಿಗೆ ಗಮನ ಕೊಡುವುದು ಸ್ಕ್ರಾಚ್ ಸಮಸ್ಯೆಯನ್ನು ಬಹಳವಾಗಿ ನಿವಾರಿಸುತ್ತದೆ.
ಡಿಕ್ಕಿ
ಸೆರಾಮಿಕ್ಸ್ನ ಗಡಸುತನ ಹೆಚ್ಚಿದ್ದರೂ, ಅವು ಸುಲಭವಾಗಿ ಒಡೆಯುವ ವಸ್ತುಗಳಾಗಿವೆ. ಬಾಹ್ಯ ಬಲದ ಪ್ರಭಾವದ ಅಡಿಯಲ್ಲಿ, ಸೆರಾಮಿಕ್ಸ್ ಸುಲಭವಾಗಿ ಬೀಳುತ್ತದೆ ಮತ್ತು ಹೊಂಡಗಳನ್ನು ಉತ್ಪಾದಿಸುತ್ತದೆ (ಚಿತ್ರ 15). ಸಾಮಾನ್ಯವಾಗಿ, ಅನಿಲಾಕ್ಸ್ ರೋಲರ್ಗಳನ್ನು ಲೋಡ್ ಮಾಡುವಾಗ ಮತ್ತು ಇಳಿಸುವಾಗ ಉಬ್ಬುಗಳು ಸಂಭವಿಸುತ್ತವೆ, ಅಥವಾ ಲೋಹದ ಉಪಕರಣಗಳು ರೋಲರ್ ಮೇಲ್ಮೈಯಿಂದ ಬೀಳುತ್ತವೆ. ಮುದ್ರಣ ಪರಿಸರವನ್ನು ಸ್ವಚ್ಛವಾಗಿಡಲು ಪ್ರಯತ್ನಿಸಿ ಮತ್ತು ಮುದ್ರಣ ಯಂತ್ರದ ಸುತ್ತಲೂ, ವಿಶೇಷವಾಗಿ ಇಂಕ್ ಟ್ರೇ ಮತ್ತು ಅನಿಲಾಕ್ಸ್ ರೋಲರ್ ಬಳಿ ಸಣ್ಣ ಭಾಗಗಳನ್ನು ಜೋಡಿಸುವುದನ್ನು ತಪ್ಪಿಸಿ. ಅನಿಲಾಕ್ಸ್ನ ಉತ್ತಮ ಕೆಲಸವನ್ನು ಮಾಡಲು ಶಿಫಾರಸು ಮಾಡಲಾಗಿದೆ. ಸಣ್ಣ ವಸ್ತುಗಳು ಬೀಳದಂತೆ ಮತ್ತು ಅನಿಲಾಕ್ಸ್ ರೋಲರ್ಗೆ ಡಿಕ್ಕಿ ಹೊಡೆಯುವುದನ್ನು ತಡೆಯಲು ರೋಲರ್ನ ಸರಿಯಾದ ರಕ್ಷಣೆ. ಅನಿಲಾಕ್ಸ್ ರೋಲರ್ ಅನ್ನು ಲೋಡ್ ಮಾಡುವಾಗ ಮತ್ತು ಇಳಿಸುವಾಗ, ಕಾರ್ಯಾಚರಣೆಯ ಮೊದಲು ಅದನ್ನು ಹೊಂದಿಕೊಳ್ಳುವ ರಕ್ಷಣಾತ್ಮಕ ಹೊದಿಕೆಯೊಂದಿಗೆ ಸುತ್ತುವಂತೆ ಸೂಚಿಸಲಾಗುತ್ತದೆ.
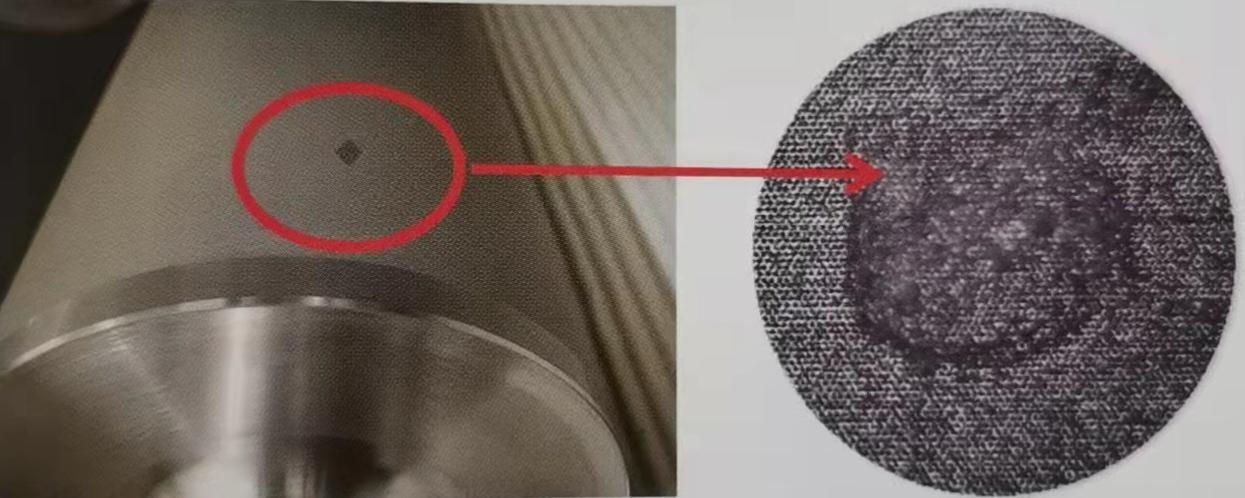
ಚಿತ್ರ 15
ಪೋಸ್ಟ್ ಸಮಯ: ಫೆಬ್ರವರಿ-23-2022